空間装飾・施工を手掛ける昭栄美術は今年秋、大型3Dプリンターを導入した。サステナビリティに大きく貢献するというこのプリンターは、最大でブース1小間ほどの造形物を創ることができる。導入を決めた専務取締役の羽山寛幸氏に話を聞いた。
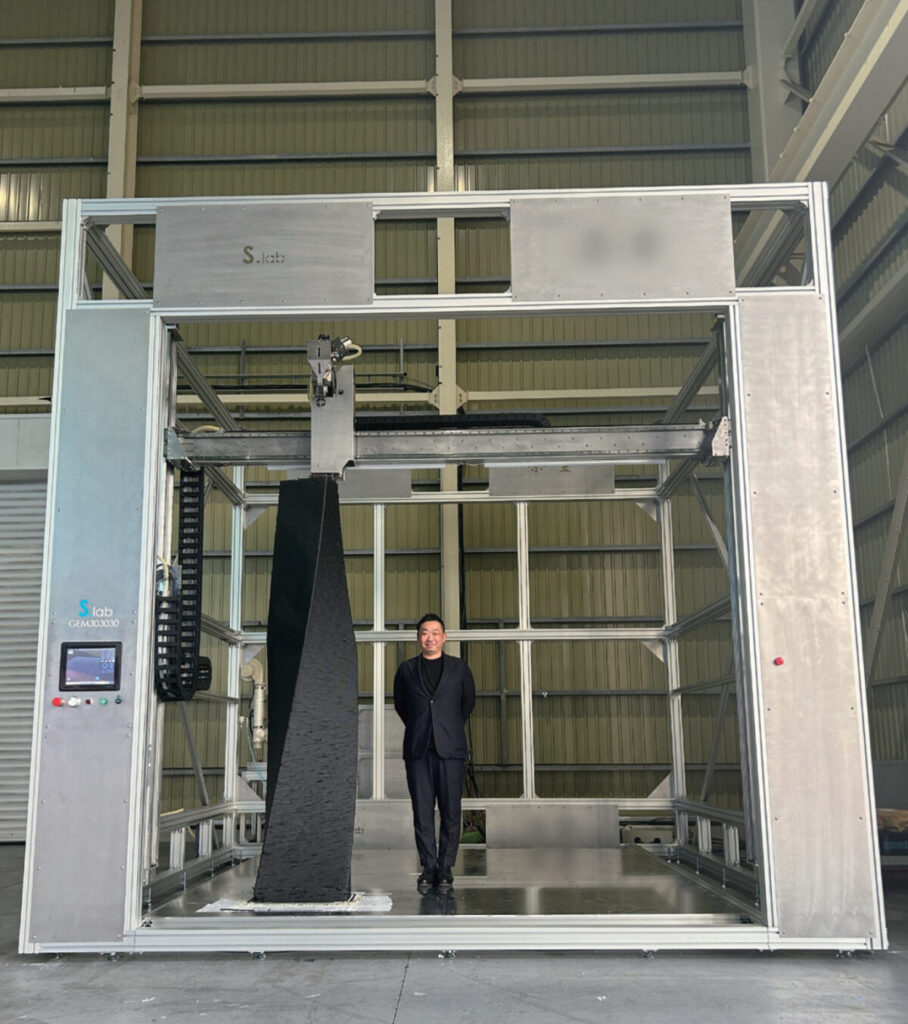
─空間装飾会社のなかでもひときわSDGsに熱心に取り組んでいらっしゃいます
当社では創業当時からムリ・ムダ・ムラを極力減らすために、5S活動や3Rを掲げて業務の効率化を図る風土がありました。例えば、安全かつ高品質の施工を提供する中での課題として、イベント現場の作業時間の制約があります。当社はベイスタジオで前もって施工を行う工程を取り入れ、現場では最終的な組み合わせのみを行うだけで良いように工程を変更しました。同時にある程度まで組み立てた状態で搬入できるトラックを特注で作りました。現場の無理を無くす、という視点から始まった取り組みですが、結果として現場作業員やトラックの数を減らし、二酸化炭素の排出量削減につながっています。
SDGsという考えが生まれたから環境に配慮した取り組みをはじめたということではなく、効率化という当たり前のこととして取り組んできたことが現代でサステナビリティという評価を受けているので、環境配慮やごみを出さないという考えは全社員に浸透しています。
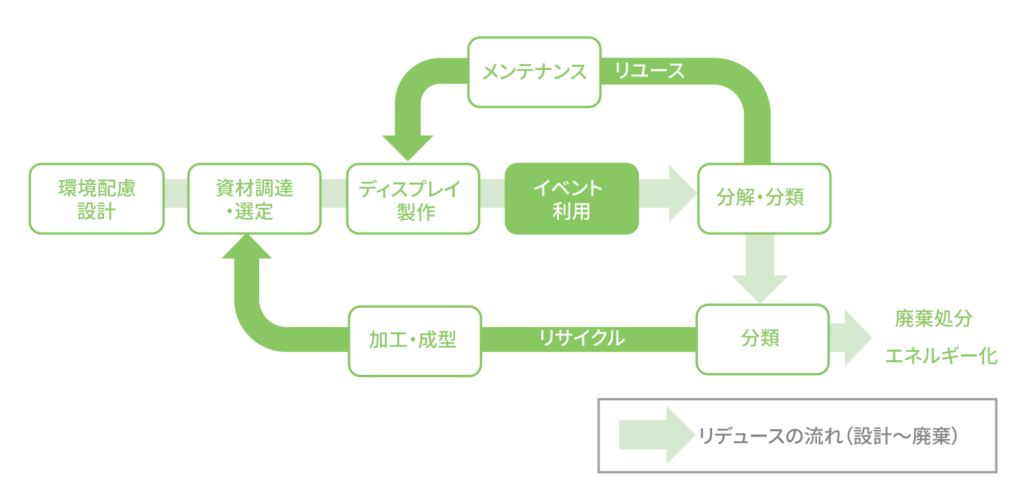
─3Dプリンターを導入した背景について教えてください
当社で提案する展示装飾の資材約80%はリユースとリデュースで構成されています。残りの約20%はそのまま再利用できないので、鉄やアルミ、切れ端の木材、ファブリックなど、素材ごとに細分化しています。
鉄は溶かして再生成へ、木材なら繊維版などに適切な処理を経て生まれ変わりますが、どうしても再加工が難しい資材は廃棄物固形燃料(RDF)にして燃料エネルギーとして循環させています。RDFも決して無駄ではありませんが、当社としてはアップサイクル率をもっと上げたかったので燃料化は最終手段にしたいという思いがありました。廃材を再利用できる方法を探し、見つけたのが今回導入した3Dプリンターです。大きな特徴はさまざまな材質に対応でき、廃材も材質として混ぜ込むことができるという点です。生成された造形物は、粉砕、生成することで材料として使いまわしできます。まさに我々の探していたものだったので導入を決意しました。
─高い注目を集めそうです
ハイブランドや大手メーカーなど、社会を牽引する立場の大企業はアップサイクルの意識が高く、展示会のブース、店舗装飾、イベントプロモーションで使う素材に対してもサステナビリティを求めます。展示会であれば、数回の出展のデザインを使いまわすことを前提にした提案のニーズも増えていますね。デザイナーも再利用を意識した提案に慣れているので、1度目のブースをパーツごとで分解し、同じ資材を使いつつも、場所を入れ替えてデザインを変える提案をこれまで行っていました。ここに3Dプリンターで作成した造形物を組み合わせると、さらにユニークな提案ができると思います。
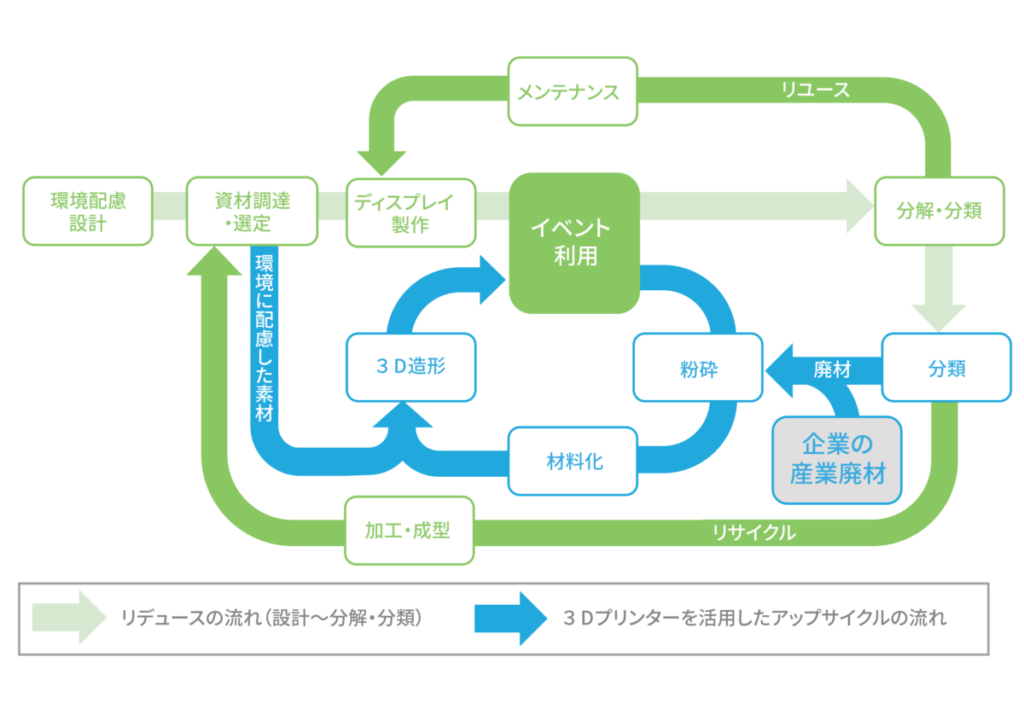
─今後の展望についてお聞かせください。どのような活躍を期待しますか
廃材の活用は業種を問わず、“アップサイクル”をキーワードにその手法に高い注目が集まっています。3Dプリンターの導入で我々も自社で出している廃材だけでなく、企業が抱える廃材に新しい価値を与えた空間を提案できるようになりました。各社が取り組むアップサイクルに貢献できればと思っています。
現場の作業負担の軽減につながるので、人手不足の問題を慢性的に抱えているイベント業界にも良い影響を与えると思います。加えて木工造作では難易度の高かった曲面、できなかった表現が容易に行えるなど、デザイン性は向上します。イベント業界は世間から“作っては壊す”という印象を持たれており、空間装飾は「簡素でシンプル=使いまわせる、質の高いデザイン=廃棄になる」というイメージがあったと思います。
今回の3Dプリンターによる循環型ディスプレイを広めていくことで業界の古いイメージを払拭し、業界の持続可能性を高めていきたいと思います。
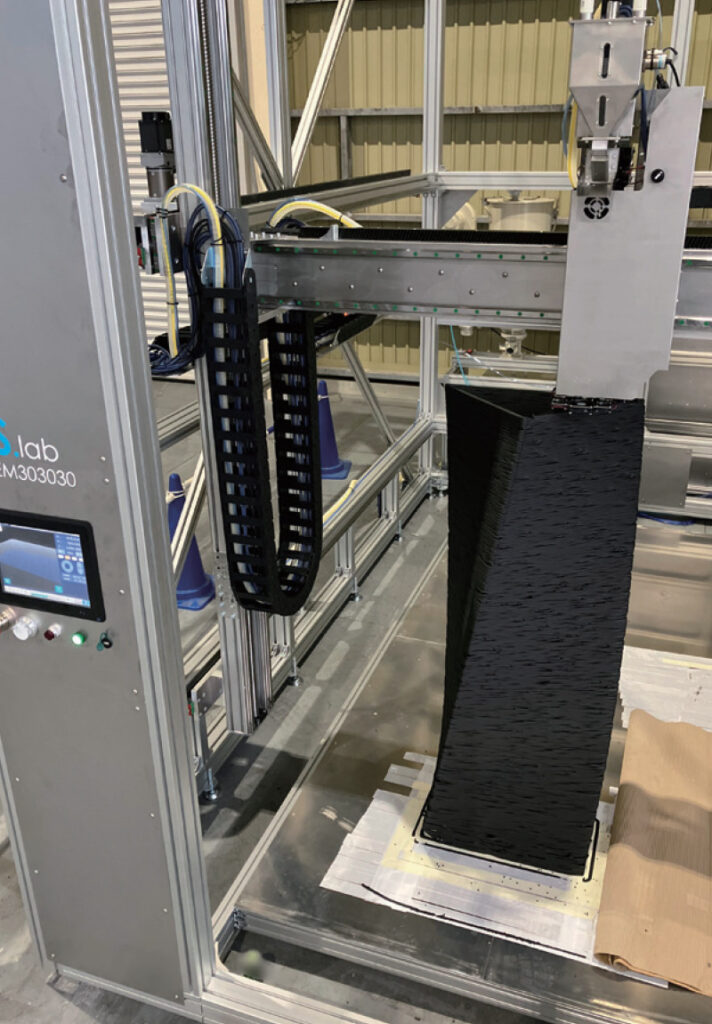